A maioria dos motores encontrados nas aplicações industriais tem alimentação trifásica. O controle da velocidade e torque desses motores diretamente a partir da rede de energia exige recursos que a tecnologia atual pode oferecer com vantagens. Um desses recursos é o inversor de freqüência que, além de possibilitar um controle preciso do torque e velocidade, proporciona muitas outras vantagens como o melhor aproveitamento da energia e o maior nível de segurança. Neste artigo veremos o que são os inversores de freqüência e como funcionam.
O que é um Inversor de Freqüência
Uma forma de se controlar com precisão torque e velocidade de um motor trifásico, quer seja a partir de uma entrada de alimentação monofásica, quer seja a partir de uma entrada de alimentação trifásica é através de um inversor de freqüência.
Os inversores de freqüência possuem uma entrada ligada à rede de energia comum de alimentação e uma saída que é aplicada ao dispositivo que deve ser alimentado, no caso um motor trifásico, conforme mostra a figura 1.
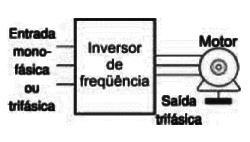
Como o controle se faz variando a freqüência e a tensão circuitos com características especiais devem ser usados.
Esses circuitos se baseiam em configurações complexas formadas por dispositivos semicondutores de potência, dispositivos lógicos de controle, sistemas de proteção e de monitoramento do funcionamento.
Para entendermos melhor como funciona um inversor típico será interessante partir de sua configuração básica, dada pelo diagrama de blocos da figura 2.
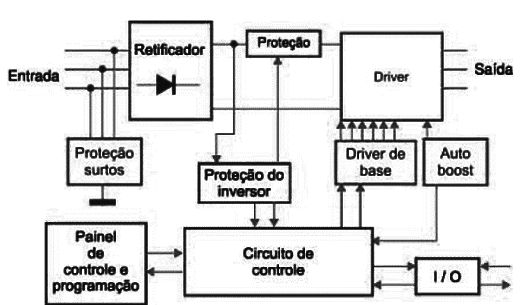
Os blocos básicos têm funções especificas e podem ter configurações levemente diferentes conforme as características elétricas finais desejadas e também a tecnologia usada pelo fabricante.
a) Retificador
Este bloco retifica a energia trifásica (alternada) disponível na entrada para a alimentação do inversor. A configuração mais comum é a de uma ponte de diodos em onda completa conforme mostra a figura 3.
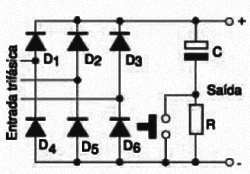
Na saída temos um capacitor para realizar a filtragem da tensão contínua obtida.
b) Inversor de potência
Aqui é gerada a tensão trifásica de alimentação do motor usando a tensão contínua do bloco anterior. Conforme mostra o circuito simplificado da figura 4, são usados transistores (IGBTs) que chaveiam a tensão a partir dos sinais de gerador PWM (Modulação por Largura de Pulso).
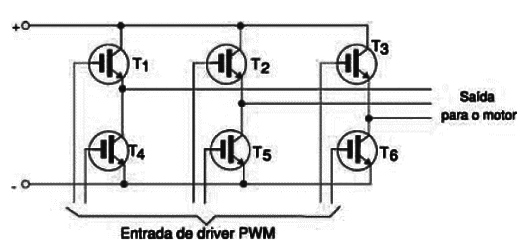
Os sinais gerados são trens de pulsos, mas ao serem aplicados numa carga indutiva como um motor, o resultado é uma forma de onda aproximadamente senoidal.
As características do próprio enrolamento do motor se encarregam de fazer uma suavização da forma de onda que se torna quase que senoidal.
c) Controle
O bloco de controle gera os pulsos que atuam sobre os transistores de chaveamento. As formas de onda e freqüência do sinal gerado por este circuito vão determinar a velocidade e potência aplicada ao motor.
Na figura 5 temos mostramos as formas de onda que encontramos neste circuito. Veja que sua aplicação numa carga indutiva resulta numa forma de onda aproximadamente senoidal.
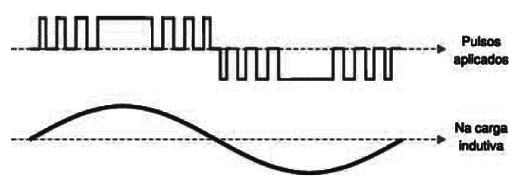
d) Proteção contra Surtos
Sabemos que a tensão da rede de energia pode conter surtos e transientes. Para a proteção desses dispositivos e do próprio circuito são usados elementos como varistores, TVS e outros componentes do mesmo tipo.
e) Proteção Interna
Este bloco monitora as tensões presentes na saída do retificador. Diante de uma variação perigosa o circuito sinaliza o bloco de controle de modo que ele possa fazer a proteção, por exemplo, desligando a alimentação.
f) Driver
Este bloco gera os sinais que excitam os transistores de potência de saída.
g) Auto-Boost
Este bloco é monitora as condições de carga do motor determinando o nível de tensão que deve ser aplicado para se gerar o torque necessário à aplicação.
h) Programação
Trata-se de um painel que apresentam informações gerais como avisos de erro e onde é feita a programação do modo de funcionamento do motor.
i) Interface (I/O)
Através deste bloco o inversor se comunica com dispositivos externos, por exemplo, um computador ou ainda microprocessadores ligados à sensores.
j) Controle
Neste bloco são tomadas as decisões em função da programação, de sinais externos e de sinais internos como os de proteção.
Chaveamento
Para analisar como o circuito gera uma tensão senoidal trifásica a partir de sinais PWM tomemos como ponto de partida o circuito simplificado da figura 6.
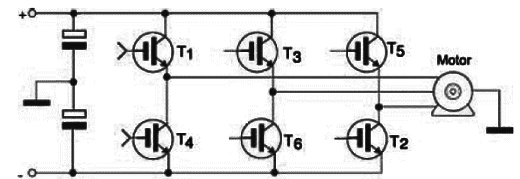
Temos então 6 transistores funcionam como chaves numa configuração em ponte.
Na operação, os 6 transistores devem ser ligados 3 a 3 de tal forma a se obter 8 combinações que resultam em três formas de onda senoidais defasadas de 120 graus.
Dessas 9 combinações existem três que são proibidas pois levam o circuito a uma condição de curto.
São aquelas em que transistores que estão em série conduzem ao mesmo tempo.
Na figura 7 temos então os pontos de chaveamento e as formas de onda correspondentes.
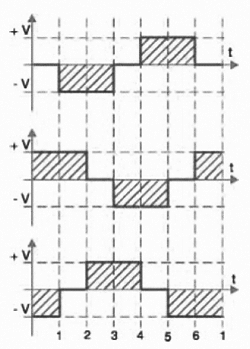
Colocando isso numa tabela temos:
Tempo | V1 | V2 | V3 | Transistores |
1 | 0 | +V | - V | T1, T2, T3 |
2 | -V | +V | 0 | T2, T3, T4 |
3 | -V | 0 | +V | T3, T4, T5 |
4 | 0 | -V | +V | T4, T5, T6 |
5 | +V | -V | 0 | T5, T6., T1 |
6 | +V | 0 | -V | T6, T1, T2 |
Observe que, se o chaveamento for feito da forma indicada serão gerados sinais defasados de 120 graus.
Controlando a Velocidade
Um inversor de freqüência possibilita o controle da velocidade de um motor trifásico através da freqüência da tensão gerada.
A freqüência de operação de um inversor normalmente está entre 0,5 Hz e 400 Hz, dependendo do modelo e da marca.
Deve-se, entretanto notar que quando a velocidade de um motor é alterada pela variação da freqüência, seu torque também é modificado.
Para se manter o torque constante basta fazer com que a relação tensão/freqüência ou V/F seja constante.
V/F = constante.
Por exemplo, se a tensão aplicada num motor for de 200 V quando a freqüência for 100 Hz (V/F = 3), alterando a freqüência para 250 Hz, a tensão aplicada deve ser 400 V.
Na figura 8 temos a curva V/F de um inversor de freqüência comum.
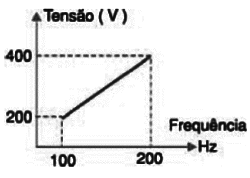
A faixa de valores de tensão e freqüência em que deve operar um motor é programada no bloco de controle.
Programar um inversor é dito “parametrizar” o inversor.
Inversores Escalares e Vetoriais
Conforme vimos, para manter o torque quando a velocidade varia basta ter a relação V/F constante.
Os inversores que seguem este padrão de funcionamento são ditos escalares.
Entretanto, em aplicações AC de freqüência muito baixa não é possível manter o torque constante em rotações muito baixas, dada a própria curva de rendimento do motor.
Para estes motores é preciso haver uma compensação mais complexa da relação tensão/freqüência, que leve em conta outros fatores como a carga do motor.
Para esta finalidade são preferidos os inversores que variam tanto a tensão como a freqüência mas segundo uma curva que leva em conta o rendimento do motor, principalmente nas baixas rotações.
Estes inversores usam tacômetros ou encoders para sensoriar a velocidade do motor, obtendo assim uma informação adicional que é processada para se gerar as tensões e freqüências de controle.
Instalação de Inversores
Existem variações como o modo como cada inversor é instalado, mas a configuração geral é a mesma. A figura 9 mostra um exemplo prático.
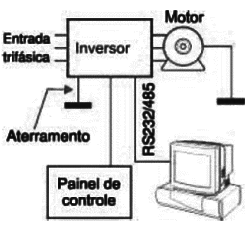
Os principais cuidados na instalação são:
a) Sempre observar a ordem das ligações. Trocas de fios podem causar a queima do inversor.
b) Se existir uma interface de comunicação RS232 ou RS485 o cabo de conexão de sinais deve ser o mais curto possível.
c) O aterramento do inversor deve ser feito com extremo cuidado. A resistência de aterramento deve ser menor do que 5 Ω (norma IEC536).
d) A ventilação do inversor seja excelente.
e) Cabos de alimentação e interface devem passar por dutos separados.
f) A qualidade da energia fornecida ao circuito deve ser observada.
g) Se dispositivos de controle como PCs, PLCs ou CNCs forem usados, devem ter terra comum com o inversor de freqüência.
h) Se cargas fortemente indutivas fizerem parte da instalação, devem ser previstos supressores de transientes e surtos.
Parametrização
“Parametrizar” um inversor é programá-lo para uma determinada modalidade de operação.
O número de parâmetros a serem programados depende da marca e tipo, sendo os mais comuns em nosso mercado os da Siemens, ABB, WEG, Yaskawa, Allen Bradley, Metaltex, etc.
Para a programação normalmente fazemos o acionamento de um certo número de teclas numa seqüência que é determinada pelo fabricante. Damos a seguir um exemplo típico:
Primeiro parâmetro – acionar tecla para ativar a entrada do parâmetro. Usamos teclas de seta para localizar o valor do parâmetro o qual é mostrado no painel. Quando o valor é encontrado, pressionando-se a tecla de entrada o valor se fixa.
Segundo parâmetro - com um novo toque na tecla, habilita-se a entrada de novo parâmetro. Depois disso, novamente com as setas, localizamos seu valor e o fixamos.
Os principais parâmetros que encontramos nos inversores são:
Parâmetro P009
Ajuste 0 – somente os parâmetros P001 a P009 podem ser alterados
Ajuste 1 – os parâmetros de P001 a P009 podem ser alterados e os demais podem ser somente lidos
Ajuste 2 – todos os parâmetros podem ser alterados exceto P009 que resseta ao ser desligado
Ajuste 3 – todos os parâmetros podem ser alterados
Parâmetro P084
Programa-se a tensão nominal do motor.
Parâmetro P083
Programa-se a corrente nominal do motor. Esse valor será usado pelo sistema de proteção contra sobrecarga.
Parâmetro P003
Programa a freqüência mínima de saída, variando tipicamente entre 0 e 650 Hz.
Parâmetro P013
Programa a freqüência máxima de saída. Pode variar entre 0 e 650 Hz.
Parâmetro P031
Programa-se a freqüência do JOG. O JOG ou impulso é um recurso usado para fazer uma máquina funcionar em velocidades muito baixas, facilitando o posicionamento de peças antes de entrar em funcionamento normal.
Um exemplo disso é a fixação de um rolo de papel na máquina antes dele fio começar a ser utilizado no processo.
Parâmetro P002
Programa a rampa de aceleração, ou seja, o tempo que o motor leva para atingir a velocidade máxima, conforme mostra a figura 10. Pode variar entre 0 e 650 segundos.
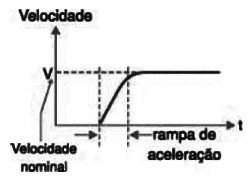
Parâmetro P003
Programa o tempo de parada.
Parâmetro P076
Programa a freqüência do circuito PWM. Esta freqüência pode variar em alguns tipos de 2 em 2 kHz. Deve ser escolhido deve o menor valor possível para que seja evitada EMI. No entanto, o uso de freqüências muito baixas pode fazer com que ruídos audíveis sejam produzidos no circuito
Conclusão
O uso de inversores de freqüência torna-se cada vez mais comum, inclusive em aplicações que fogem à indústria como o controle de sistemas de ar condicionado, etc.
Com eles, além do controle preciso dos motores temos um aproveitamento melhor da energia e muito mais segurança.