"Seguir à risca todas as instruções, nem sempre significa a certeza de se obter êxito completo numa montagem, se as soldagens forem malfeitas. Muitos principiantes — e mesmo veteranos — têm se decepcionado, justamente pelo fato de não darem a importância devida a este pormenor: Se esse for seu caso, se algum dia um aparelho que você montou não chegou a resultados satisfatórios sem que houvesse motivo aparente, então este artigo deve ser lido e estudado com o máximo de atenção".
(*) O artigo saiu numa revista de 1975.
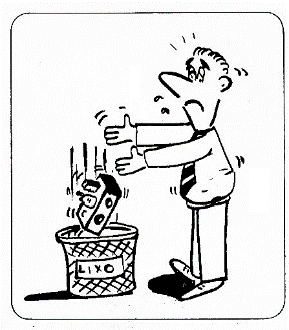
Uma boa soldagem é essencial para o bom funcionamento de qualquer equipamento eletrônico, por mais simples que seja. A execução de uma soldagem bem-feita exige, entretanto, cuidados especiais que, embora simples, podem significar a diferença entre o êxito e o fracasso de uma montagem.
Por que a solda?
As conexões' soldadas nos equipamentos eletrônicos são feitas com 2 finalidades: suportar o próprio componente, servindo, portanto, como junção mecânica, a fornecer uma conexão elétrica, permitindo que as correntes possam atravessá-las sem dificuldade.
Com relação à primeira finalidade, como em equipamentos comuns não há preocupação com. uma resistência mecânica elevada, já que os componentes são, em geral, bastante leves (tais como resistores, transistores, etc.), a solda visa muito mais o estabelecimento do contato elétrico do que propriamente urna resistente fixação do componente.
Por esse motivo, a obtenção de uma conexão elétrica perfeita é que realmente se torna importante. Qualquer falha na operação de soldagem pode significar em chamadas "soldas frias" que fazem com que junções aparentemente bem-feitas apresentem urna resistência à passagem da corrente suficientemente elevada para prejudicar o desempenho do equipamento.
A solda
A solda normalmente usada em trabalhos práticos de eletrônica é do tipo brando, consistindo numa liga de estanho (Sn) e chumbo (Bb).
O chumbo se funde a uma temperatura de ± 327°C (quando puro), enquanto que o estanho se funde a uma temperatura de H- 232°C (quando puro); mas, quando misturamos esses dois metais, formando a liga, conforme a proporção em que se realizar essa mistura, podemos obter gradativamente ligas de pontos de fusão mais baixos. O ponto mínimo, ou seja, a liga de menor ponto de fusão é a obtida pela mistura de aproximadamente 60% de estanho com 40% de chumbo. Nestas condições, essa liga se funde a pouco menos de 190°C, sendo essa, justamente a liga usada como solda em trabalhos de eletrônico. A solda comum é, portanto, conhecida como solda 60/40, dada a proporção de chumbo e estanho de que é formada.
É importante notar que, ao aquecermos a solda comum até seu ponto de fusão, ela não passará imediatamente pana o estado líquido, mas - apresentará um estado pastoso intermediário. Esse estado pastoso deve ser evitado nos trabalhos práticos, o que significa que deveremos sempre usar a solda aquecendo-a bem acima do seu ponto de fusão, justamente para evitar esse estado intermediário.
Os ferros do soldar (soldadores)
Os ferros de soldar de que podemos dispor são dos mais diversos tipos, operando segundo diferentes princípios, cuja quantidade de calor obtida abrange uma gama de valores bastante grande.
A quantidade de calor que um soldador pode aplicar a uma junção é função das dimensões dessa junção. Quanto maior for o volume da junção a ser soldada, ou ainda, quanto maior for a dispersão de calor por irradiação para componentes próximos, maior deve ser a quantidade de calor que deve ser aplicada ao local para que ela possa ser aquecida à temperatura que se necessita para se obter a fusão completa da solda. É importante notar que apenas a junção deve ser aquecida, devendo-se, em muitos casos, evitar a qualquer custo que o calor possa atingir o corpo do componente que está sendo soldado, ou os componentes próximos.
Deste modo, enquanto que, para a soldagem de um componente pequeno como um transistor, ou um resistor a uma ponte de terminais de latão pelos próprios terminais, um ferro de pequenas dimensões será o bastante; para a soldagem de um fio grosso de cobre ao chassi, um ferro de maior potência será necessário.
Para orientação do leitor podemos dar uma divisão, por categorias, dos soldadores que devemos ter nas bancadas, com os trabalhos a que se destinam. Evidentemente, devemos lembrar que não se trata de uma divisão rigorosa, já que a aplicação dessa ferramenta em cada caso depende também da habilidade e dos conhecimentos do operador.
a) Ferros de pequena potência (até 30 Watts) que são usados normalmente na realização de junções pequenas, na soldagem de semicondutores (tais como transistores e circuitos integrados) e, em trabalhos em placas de fiação impressa.
b) Ferros de média potência (entre 30 e 100 Watts) — são usados na soldagem de componentes e junções em que a quantidade de calor necessária seja maior do que aquela que um ferro pequeno possa fornecer; são usados, por exemplo, em conexões de fios grossos, na ligação de fios a pontes de terminais volumosas, conecto: res, etc.
c) Ferros de grande potência (acima de 100 Watts) — são usados para conexões em que se necessita de quantidade de calor acima do normal como por exemplo na soldagem direta de fios, componentes, ou pontes ao chassi de um equipamento (coisa que na eletrônica moderna "já era"!). Se dividirmos os montadores em categorias, podemos sugerir para cada um, os seguintes soldadores, como ferramentas obrigatórias na bancada de trabalho:
a) Estudantes e principiantes: um soldador de pequena potência de até 30 Watts com jogo de pontas; com este, a maioria das montagens simples poderá ser executada sem maiores problemas.
b) Profissionais em início de carreira, experimentadores avançados: um soldador de pequena potência (até 30 Watts) e um de média potência (até 100 Watts).
c) Profissionais avançados; montadores bastante ativos: um soldador de pequena potência (até 30 Watts) com jogo de pontas, uma de média potência (até 100 Watts), um de grande potência (200 Watts) e 1 pistola de soldar.
A soldagem
Para a realização de uma conexão soldada, em primeiro lugar o soldador deve ser aquecido à sua temperatura normal de trabalho. Se ele for de pequena potência, uns 5 minutos bastarão para isso; se sua potência for maior, uns 10 minutos, pelo menos, deverão ser aguardados.
Uma vez na temperatura ideal, a ponta do ferro deverá ser "estanhada", ou seja, recoberta como urna fina camada de solda, para facilitar a transferência de calor e adesão de solda nas peças a serem soldadas. Para estanhar a ponta do ferro de soldar, em primeiro lugar deveremos limpá-la, removendo a camada de óxido com uma lima ou lixa fina. Em seguida esfregamos o fio de solda, vagarosamente, sobre a sua ponta, de modo que ela se funda e se espalhe, recobrindo-a conforme mostra a figura 1.
A seguir, para soldagem dos componentes propriamente ditos, o leitor deve sempre ter em mente os "10 Mandamentos do Bom Soldador".
Mandamentos do bom soldador
1) A ponta do ferro de soldar deve estar sempre estanhada, pois somente assim será garantida uma rápida transferência de calor para a junção a ser realizada; deve ser constantemente limpa com um pano úmido, lixa fina ou escova de latão e novamente estanhada (fig. 2). 2) O calor deve ser aplicado, em primeiro lugar, às peças a serem soldadas; somente depois de aquecidas suficientemente, é que deve ser encostada a solda à junta: esta, então, fundir-se-á imediatamente, espalhando-se pela junção.
A operação deve ser feita com o máximo cuidado e. rapidamente para que o calor desenvolvido no processo não atinja o componente que está sendo soldado (fig. 3).
3) Ao se soldar um fio, ou terminal da componente, a uma ponta ou placa de fiação impressa nunca enrole os terminais do componente ou o fio em torno do local em que vai ser soldado. A solda por aí só oferece uma resistência mecânica mais do que suficiente para sua sustentação. O motivo pelo qual não se devem enrolar os terminais é que a tarefa de se retirar o componente em caso dé necessidade de substituição se torna extremamente difícil se ele estiver enrolado ao terminal além de soldado (fig. 4).
4) Antes de soldar fios que não sejam do tipo previamente estanhados (fios esmaltados, por exemplo), ou peças sem terminais também estanhados, as junções têm de ser preparadas para receber a solda, devendo para isso, os terminais serem limpos com unia lixa fina. O terminal, peça ou fio deve ser limpo até ter completamente removida a camada de óxido ou gordura que eventualmente a cubra, o que será reconhecido quando adquirir um brilho metálico intenso (fig. 5).
5) Para soldar peças de tamanho considerável, elas devem ser previamente estanhadas no ponto em que se for realizar a junção, sendo o mesmo coberto por uma camada de solda (fig. 6).
6) Nunca deve ser usada solda em excesso, pois neste caso, a quantidade de calor necessário à sua fusão poderá ser tão elevada que o ferro usado poderá "não dar conta". A solda adquirirá um estado pastoso, não se realizando, consequentemente, uma boa junção. A solda realizada deste modo tem uma aparência fosca, sendo reconhecida facilmente por isso (fig. 7).
7) Quando forem soldados fios isolados com capa plástica, a solda deve ser realizada o mais rapidamente possível para que o calor desenvolvido não derreta seu isolamento. O soldador, nestas condições, deve estar bem quente para que a aplicação de calor ao ponto de conexão seja a mais rápida possível. O fio a ser soldado, não deve ter seu isolamento cortado nem muito próximo, nem muito longe do ponto de conexão (fig. 8).
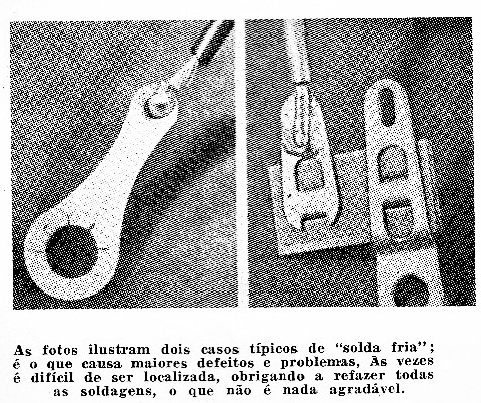
8) Ao retirar o ferro de soldar da junção soldada, devemos deslizá-lo piara o lado e não o retirar puxando-o para cima. Isso tem a finalidade de se evitar a formação do "bico" de solda que é bastante antiestético (fig. 9.
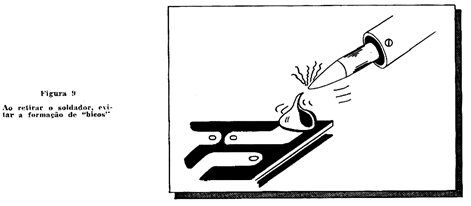
9) Quando soldar componentes, não permitir qualquer movimento destes antes da solda estar completamente rígida. Pode-se reconhecer o momento em que isso ocorre, pelo fato de a solda perder seu brilho, ficando com uma aparência branco-fosca, porém lisa. Em geral, o tempo de resfriamento para pequenos componentes é de uns 5 segundos (fig. 10).
10) Se for usada alguma pasta para soldar, o que a todo o custo deve ser evitado, após a realização da junção, a pasta deve ser removida. Isso pode ser feito facilmente por meio de um pano embebido em álcool. Caso essa providência não seja tomada, o ácido eventualmente existente na pasta pode afetar a peça, corroendo-a após algum tempo (fig. 11).
Seguindo as recomendações que a prática descrita nos ensinou, você poderá aprender a soldar ou corrigir defeitos e erros adquiridos por mau ensino ou má orientação.