A tendência atual é uma miniaturização cada vez maior com mais funções reunidas num único chip. Isso significa uma dificuldade cada vez maior em se projetar invólucros que, ao mesmo tempo em que sejam pequenos tenham o maior número possível de terminais. As tecnologias Quad Flat Pack (QFP) estão chegando a um ponto perigoso em que os terminais, por serem cada vez menores se tornam mais frágeis. A tendência é portanto a utilização maior da tecnologia Ball Grid Array (BGA) que elimina estes terminais e pode levar a invólucros muito compactos com grande quantidade de pontos de ligação. Veja neste artigo um pouco desta tecnologia que deve predominar nos encapsulamentos dos próximos anos. (2003)
Além das vantagens apregoadas na introdução existem diversas outras que a tecnologia BGA (Ball Grid Array) apresenta em relação aos invólucros QFP e outros, quando se pensa em montagem em superfície.
Uma delas é o espaço ocupado na placa, já que as conexões não ficam em terminais ao lado do invólucro, mas sim sob o componente, o que permite ganhar espaço
Desta forma, com os terminais por baixo do componente, nenhuma área lateral, além daquela que corresponde ao próprio componente, é ocupada na placa de circuito impresso.
Outra vantagem está na própria densidade dos pontos externos de ligação que podem ser observadas no gráfico comparativo da figura 1.
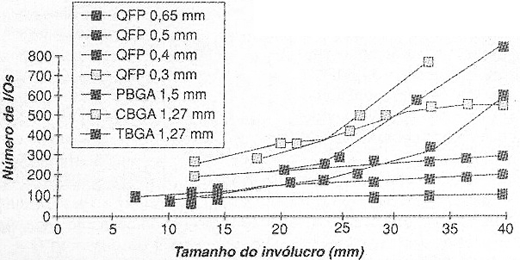
Os valores em mm são para a separação entre os terminais ou pontos de ligação nos tipos de invólucros comparados.
Veja que o aumento do número de terminais não segue uma proporção linear com o aumento do tamanho do componente.
Finalmente podemos dizer que os invólucros BGA têm uma capacidade de dissipação muito maior.
A utilização de um revestimento externo metálico que pode ficar em contacto direto com um dissipador de calor aumenta a capacidade de dissipação dos componentes que utilizam encapsulamentos BGA.
Em função destas vantagens, as aplicações dos BGAs se concentram justamente nos casos em se necessita de um elevado número de pontos de ligação com os circuitos externos ou pontos I/O e uma dissipação de potência também alta devido ao número de funções integradas.
Podemos citar os seguintes casos:
Microprocessadores
Microcontroladores
DSPs
Memórias
Gate Arrays
Chipsets
O que é a tecnologia BGA?
Basicamente podemos dizer que se trata de uma tecnologia de invólucro de circuitos integrados para componentes ativos destinada a aplicações que tenham montagem em superfície e que necessitam de elevado número de conexões externas ou I/Os.
Trata-se do que se denomina Area Array Package, ou seja, uma técnica que emprega toda a superfície de contacto do componente para as interconexões.
Conforme vimos, nenhuma área lateral ao componente é ocupada pelos terminais de ligação.
As interconexões, conforme podemos ver pela figura 2, são feitas por bolas ou esferas de uma liga de solda e eventualmente de outros metais que possam formar junções.
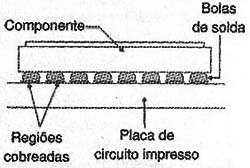
Os invólucros BGA devem atender a um certo número de especificações como por exemplo:
O comprimento do corpo do invólucro, que na maioria dos casos é quadrado, deve variar entre 7 e 50 mm.
O número máximo de terminais é 1000, mas a faixa mais comum nas aplicações atuais é a que está compreendida entre 50 e 500 terminais.
A distância centro a centro das bolas de contacto, denominada tecnicamente “pitch” varia entre 1 e 1,5 mm.
A altura depende das diversas variações deste tipo de invólucro que existem no mercado.
Com o Surgiu o BGA
A tecnologia PBGA (Plastic BGA) foi desenvolvida em 1949 pela Motorola e a Citizen, como prosseguimento de uma ideia similar adotada pela IBM e a Motorola alguns anos antes quando criaram o CBGA (Ceramic BGA).
O uso deste tipo de invólucro se difundiu no meio dos anos 90 pela Motorola e pela Compaq que os utilizou em seus computadores.
Quando foi lançado o PBGA foi chamado de Over Molded Pad Array Carrier ou OMPAC e logo em seguida uma infinidade de variações do mesmo invólucro apareceram no mercado.
Variações
Podemos citar a TBGA (Tape BGA) a SBGA (Super BGA) e até mesmo o módulo multi-chip ou MCM-BGA que é semelhante aos BGAs comuns mas que no mesmo invólucro contém diversos chips.
Na figura 3 mostramos um gráfico em que as diversas variações do tipo original de invólucro BGA são apresentadas.
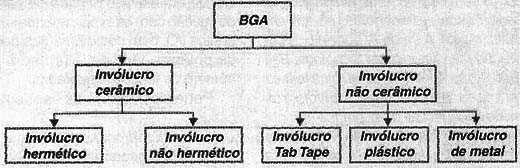
Para os usuários as diferenças não aparecem, mas para o projetista sim.
Atualmente, a mais popular de todas, tanto pelo seu custo como por outras vantagens que apresenta é a PBGA (Plastic BGA).
Para o PBGA a bola de solda consiste numa liga tipicamente de Sn-Pb.
Na figura 4 mostramos uma vista em corte de um invólucro OMPAC BGA.
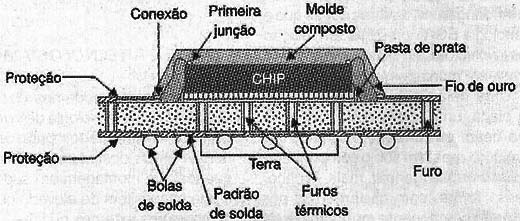
O substrato normalmente é feito de 0,25 mm de vidro epoxi laminado com uma camada de cobre de 18 um de espessura.
Um outro tipo de invólucro, menos comum, de BGA é o TBGA ou Tape /Tab BGA mostrado na figura 5.
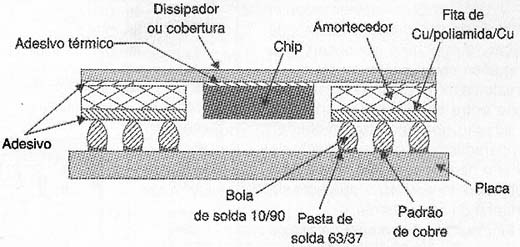
Este invólucro se baseia na utilização de um filme flexível de poliamida com uma metalização em cobre nas duas faces.
As esferas de solda para conexão são feitas de uma liga 10Sn90Pb.
Como apenas uma face do filme PI funciona como plano de terra, este invólucro se caracteriza por uma performance boa em termos de baixo nível de ruído.
O filme PI normalmente tem uma espessura de 50 um e o diâmetro das esferas de soldagem é da ordem de 0,63 mm para um pitch do invólucro de 1,27 mm.
A parte de cima do invólucro pode ser colocada em contacto direto com um dissipador de calor utilizando-se um adesivo termicamente condutivo, para esta finalidade.
Trata-se de um invólucro que possibilita uma elevada dissipação de calor, quando comparado com os invólucros plásticos.
O próximo invólucro a ser considerado é o Super BGA ou SBGA, mostrado em corte na figura 6.
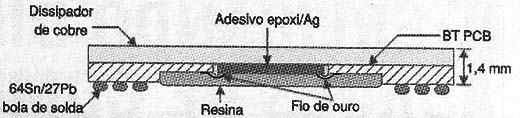
Este invólucro possibilita um excelente desempenho elétrico além de uma elevada capacidade de dissipação de calor.
Como no TBGA esta tecnologia utiliza uma placa de metal como dissipador, conectada na parte de cima do chip para facilitar a dissipação de calor e também de blindagem.
Retrabalho
O maior problema que ocorre no retrabalho com os invólucros BGA está na sua sensibilidade a poluição.
Os estudos recomendam diversos procedimentos, normalmente envolvendo equipamentos semi-automatizados.
Este trabalho envolve a aplicação de líquidos especiais, aquecimento e preparação para remoção e instalação do componente.
Uma recomendação especial é que os componentes devem ser usados antes de 8 horas depois de sua retirada das embalagens especiais.
Uma característica importante dos BGAs é que dada sua construção robustas eles apresentam menos defeitos do que ocorre no retrabalho com invólucros QFPs.
Os principais problemas que podem ocorrer no retrabalho estão relacionados com o desalinhamento dos pontos de solda, conforme mostra a figura 7.
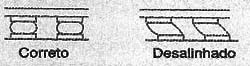
Outros problemas são os relacionados com a pressão aplicada na soldagem, a composição da liga, aquecimento, etc.
Mas, o problema mais grave que pode ocorrer no retrabalho é a formação de pontes entre os pontos de solda, conforme mostra a figura 8.
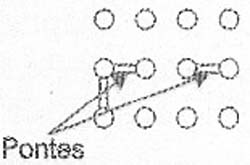
A baixa capacidade de adesão das esferas de solda é uma das principais causas da formação destas pontes.
Outras causas estão na movimentação indevida do componente no momento da solda, desalinhamento da máquina de montagem, etc.
Também deve ser considerada a falta de solda ou “solda fria” causada pela não coplanaridade da placa, composição indevida da solda, tamanho da esfera de solda, etc.
Vantagens
A substituição de componentes em invólucros QFP por equivalentes em invólucros BGAs não significa apenas a obtenção de maior número de pontos de conexão (pinos) em menor espaço como também um ganho no processo de fabricação.
Custo, confiabilidade, inspeção e retrabalho são alguns dos pontos fortes que impulsionam para o uso desta tecnologia.
Na escolha desta tecnologia para a fabricação de um produto devemos estar atentos para os seguintes aspectos que podem significar vantagens tanto em termos de desempenho como custo:
Economia de espaço nas placas de circuito impresso.
Aumento da performance
Possibilidade de uso de dispositivos com maior capacidade de dissipação de potência
Custos menores de produção
Confiabilidade
Em conseqüência, existem alguns pontos básicos que precisam ser cuidadosamente analisados, pois existem ao lado das vantagens também as desvantagens.
Vamos relacionar algumas das vantagens e das desvantagens:
Vantagens:
Os BGAs têm propriedades elétricas melhores dos que os invólucros QFPs equivalentes.
Os BGAs são menos frágeis e mais fáceis de manusear antes e durante o processo de montagem.
O processo de fixação é mais fácil e mais confiável do que os QFPs.
Os invólucros menores possibilitam a obtenção de um grau maior de miniaturização.
Desvantagens:
Existem problemas de custos associados ao roteamento das ligações nas placas de circuito impresso.
Os BGAs são mais sensíveis a sujeira
A inspeção das ligações não pode ser feita visualmente. É preciso usar equipamentos de raios-X que são muito caros.
Para os componentes muito grandes existe o problema da coplanaridade, isto é, provocada por pequenas ondulações da placa que podem causar “soldas frias”.
O retrabalho em nível de placa é muito difícil.
Normas
A principal norma que rege a utilização dos BGAs é a J-STD-013 publicada em 1996.
Esta norma inclui diversos itens importantes como o projeto de aplicações, performance, métodos de teste, técnicas de retrabalho e reparação, tipos de fluxos usados na montagem e muito mais.
Conclusão
Para invólucros com menos de 250 pinos ainda é mais vantagem usar componentes com a tecnologia QFP que são de menor custo.
Para número maior de conexões, entretanto, tanto a maior confiabilidade como o menor espaço ocupado começa a pesar para o lado dos invólucros BGAs.